High-tech facility produced record high of 15,000 components in 2021; Additive manufacturing converts 3D CAD models into physical parts
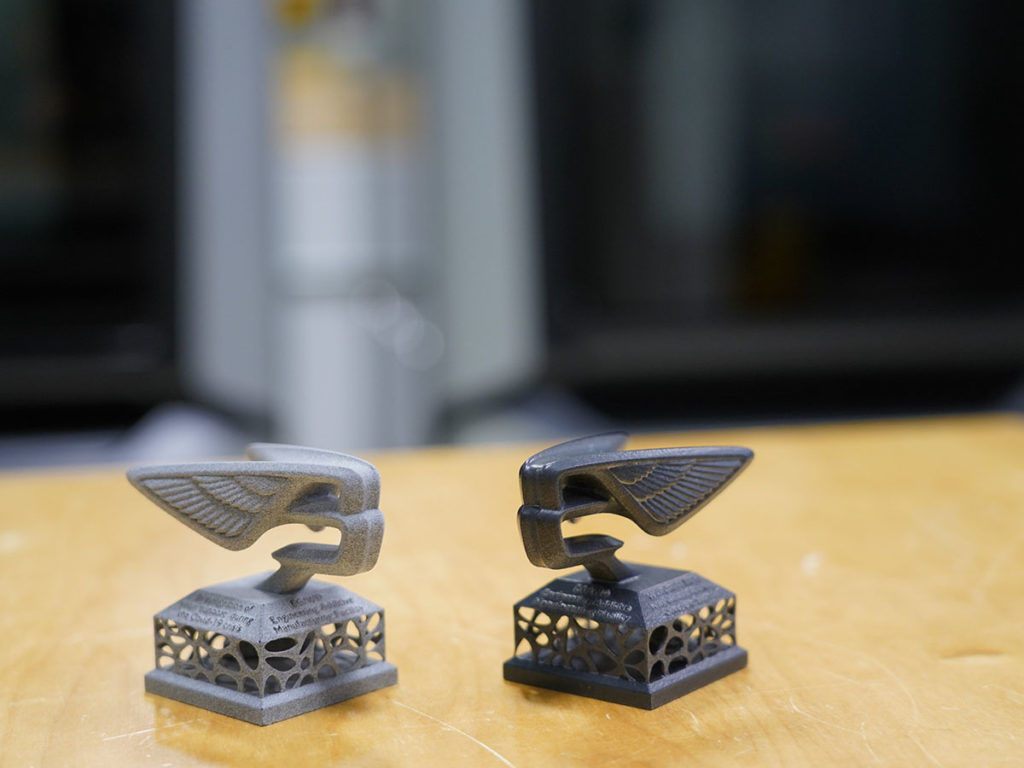
Bentley Motors has shared details of the impact of a UK£ 3mn investment to double its Additive Manufacturing (AM) capacity at the company’s headquarters in Crewe, England, where all Bentley models are built.
A state-of-the-art AM facility has been applied to a wide range of uses, producing more than 15,000 components in 2021 alone. This expansion will also enable Bentley to utilise advanced technology to create 3D printed vehicle components and even greater personalisation in customer cars.
The AM systems convert 3D CAD models into physical components and is recognised as one of the fastest developing technologies in the world. Bentley’s innovative research and development team has already identified a wide variety of items to print, including on-the-job assisted tools for manufacturing colleagues, such as lightweight sanding blocks in Bentley’s iconic wood shop.
AM has been employed to create physical components for several prototype Bentleys, including full-scale powertrain models and aerodynamic wind tunnel models. The advanced techniques have also been used to produce parts for the record-breaking Bentley models that were driven in the demanding Pikes Peak Challenge in America. “Bentley’s approach to additive manufacturing is industry-leading and the facility is quickly becoming a cornerstone of our ‘Dream Factory’ ambitions. One of the key benefits is that it is efficiency led, cutting down on the cost and complexity of a myriad of jobs,” commented Peter Bosch, Bentley’s Member of the Board for Manufacturing.
Want to stay updated on the latest industry news and trends? Subscribe today to receive your monthly news highlights directly in your inbox!